Le moulage par injection est essentiel à la fabrication en série de pièces en plastique élaborées. Pour créer des produits de la plus haute qualité à moindres coûts, on a jusque-là privilégié les systèmes avancés de refroidissement pour matériaux fondus. Il s’agit néanmoins d’un processus ardu et chronophage, même pour un ingénieur compétent. La conception automatisée des canaux de refroidissement pourrait-elle faciliter le travail des ingénieurs ?
C’est justement ce sur quoi parie la filiale Life Solutions Company de Panasonic Corporation. L’entreprise japonaise a mis au point une nouvelle méthode de production des canaux de refroidissement à eau de leurs moules, en se servant d’une imprimante 3D hybride capable d’imprimer du métal. En combinant la fabrication additive et le fraisage, on parvient à produire un système de refroidissement conforme qui dispose les canaux en fonction de la forme des pièces. On réduit ainsi de 20 % le temps de refroidissement par rapport aux dispositifs classiques, où les canaux sont forés directement dans le moule.
Seiichi Uemoto est l’un des analystes du Centre d’ingénierie de production de Panasonic, où l’on conçoit et fabrique les moules. Il enseigne les différentes méthodes de conception et soutient le développement des compétences en ingénierie assisté par ordinateur (IAO) pour faire connaître les techniques avancées utilisées dans son domaine.
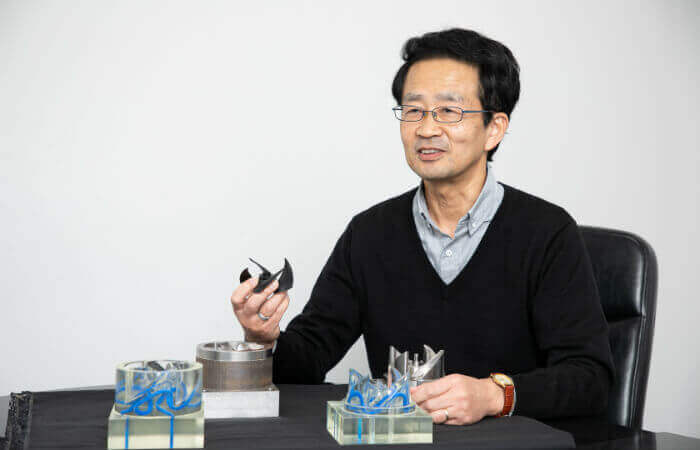
Alors qu’il tentait d’optimiser la conception des circuits de refroidissement des moules métalliques en forme de boîte, il a eu l’idée d’utiliser les données de gauchissement des pièces produites pour analyser les écarts entre les canaux. Cette étude l’a ensuite poussé à essayer d’automatiser la conception des moules métalliques.
« Je me suis dit qu’avec les bons paramètres, je pourrais me servir de la conception générative pour créer automatiquement les canaux de refroidissement des moules », explique-t-il. En effet, l’analyste a compris que la conception générative employait l’analyse structurelle et produisait efficacement des pièces plus légères.
« L’optimisation topologique ne peut produire qu’un seul résultat avec les paramètres qu’on lui fournit, continue-t-il, et il est difficile d’obtenir des pièces aux contours lisses à partir de ce résultat. J’ai alors compris que la conception générative pouvait radicalement remédier à cela et proposer efficacement une multitude de concepts tout en tenant compte des principes de fabrication. »
Un processus aidé par la conception générative
Ainsi, Seiichi Uemoto espérait pouvoir créer de nouveaux moules et automatiser le processus de conception grâce à la conception générative. À l’heure actuelle, les ingénieurs les plus qualifiés de l’entreprise créent plusieurs produits à l’aide du logiciel Moldflow d’Autodesk, qui permet de simuler le processus d’injection et d’affiner la forme des moules. « L’idée était d’utiliser la conception automatisée pour anticiper certains aspects du processus auxquels les concepteurs n’auraient peut-être pas pensé, et faciliter ainsi leur travail. », précise-t-il.
Pour ce faire, Panasonic a fait appel à l’équipe d’experts d’Autodesk de Birmingham, en Angleterre. L’objectif était d’utiliser la conception générative afin de mettre au point les canaux de refroidissement à eau des moules. Pour effectuer ses tests, l’équipe a choisi les pales que l’on trouve dans les dispositifs de ventilation et qui sont déjà produites en série.

Ces pales sont petites et leur forme est complexe. Un expert en conception a soumis plusieurs contraintes pour créer leur forme initiale, générer les canaux de refroidissement, et empêcher que le parcours des canaux influence les détails les plus fins des pièces moulées.
Au cours du processus de conception, la forme des pales a évolué de nombreuses fois, jusqu’à ce qu’il ne reste que les composants essentiels à la réalisation des canaux de refroidissement requis. Seiichi Uemoto craignait que le logiciel ait du mal à améliorer l’efficacité du modèle d’origine, car les moules des ingénieurs de Panasonic étaient déjà très précis. « J’ai néanmoins été très impressionné par les itérations très complètes que le logiciel a automatiquement générées », commente-t-il.
Par ailleurs, l’agencement des canaux de refroidissement était encore plus surprenant. Certains d’entre eux, qui devaient longer la couche externe du moule, étaient soudainement organisés d’une toute nouvelle manière. L’analyste admet qu’il n’avait jamais pensé procéder ainsi : « Personne n’aurait pu imaginer des formes comme celles élaborées par la conception générative. »
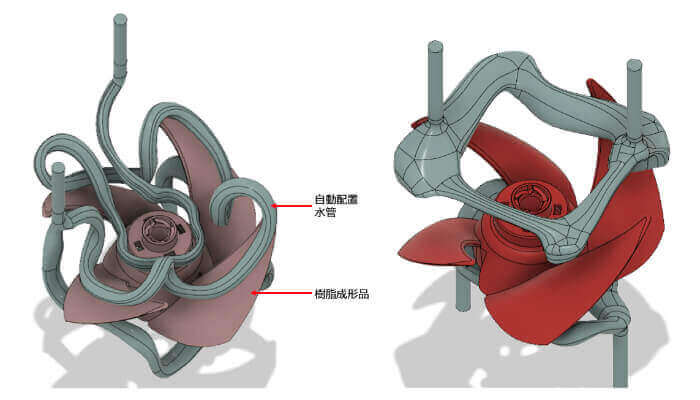
La preuve par l’exemple
Ce processus a donné lieu à la fabrication de quatre prototypes : le cas B, soit la pièce d’origine conçue par un ancien ingénieur et qui est utilisée en usine ; le cas C, réalisé à l’aide de la conception générative et basé sur la pièce d’origine ; le cas D, réalisé à l’aide de la conception générative et dont la forme est soumise à moins de contraintes ; et le cas E, identique au cas C, mais contenant davantage de canaux de refroidissement. L’équipe a ensuite minutieusement mesuré les pièces produites à partir de ces prototypes afin d’évaluer les performances de chaque moule.
Cette évaluation a montré qu’il y avait très peu de différence entre les moules dont les canaux de refroidissement avaient été générés automatiquement et le moule réalisé selon les méthodes traditionnelles. « J’ai pu constater que la conception était élaborée de sorte à façonner les pièces à partir des changements de température à l’intérieur des moules, explique Seiichi Uemoto. Ce fut une véritable découverte. En fin de compte, la fabrication assistée par ordinateur et la conception automatisée nous ont permis d’obtenir des pièces aux contours lisses, ce qui était notre objectif. »
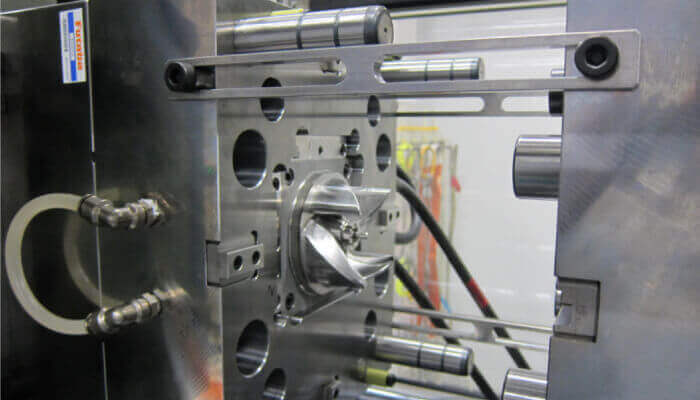
Un ingénieur expérimenté a besoin d’environ huit heures pour concevoir un moule, et il n’existe actuellement aucun moyen de simplifier ce processus, quel que soit le niveau de compétence du concepteur. Malgré tout, Seiichi Uemoto s’attend à ce que le succès de ce projet donne naissance à de nouvelles techniques qui permettront d’alléger le travail de ces ingénieurs.
« C’est un grand pas en avant, se réjouit-il. Si nous pouvions maintenant mettre au point un logiciel capable d’intégrer cette nouvelle méthode de production, nous pourrions accélérer le processus et créer des programmes davantage axés sur le contrôle de la température, ce qui devrait profiter à une multitude d’utilisateurs et d’utilisations. »