La fabrication additive (FA) est un terme large pour un processus de production dans lequel un objet est produit « en ajoutant un matériau couche après couche (et non en soustrayant de la matière comme dans le cas de l’usinage conventionnel) ». Jusqu’à présent, il existe sept types de processus AM, parmi lesquels les plus populaires sont : FDM, SLA et SLS.
FDM – Modélisation des dépôts fondus
La modélisation par dépôt fondu (FDM), également connue sous le nom de FFF (fabrication de filaments fondus), est la technologie la plus connue et fait partie du processus d’extrusion de matériau. Il utilise des matériaux thermoplastiques, généralement sous forme de bobines de filaments. La buse chauffée de l’extrudeuse fait fondre le matériau qui est ensuite déposé sur un substrat. Le FDM présente plusieurs avantages. Le processus d’impression est facile à apprendre, moyennement rapide et ne nécessite généralement pas beaucoup d’espace. La majorité des imprimantes sont de la taille d’un bureau, ce qui les rend idéales pour le bureau. Mais d’un autre côté, les FDM sont également utilisés comme de grosses machines industrielles, pour soutenir les processus de fabrication. Dans de tels cas, la forme de pastille du matériau de construction peut être utilisée plutôt qu’un filament.
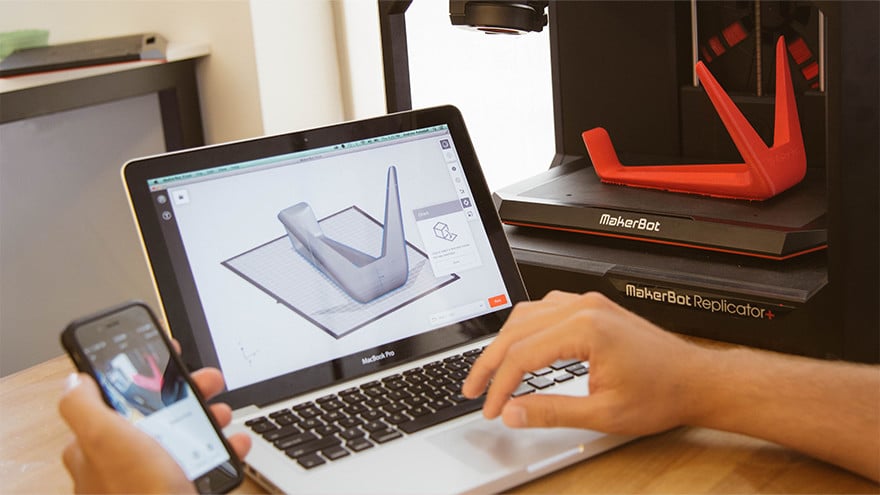
Les entreprises et les utilisateurs individuels utilisent FDM pour créer des prototypes fonctionnels, des modèles de concept de produit ou des outils rapides. Les modèles médicaux sont de plus en plus populaires car certains producteurs ont obtenu l’approbation de la FDA.
Conception pour FDM
Pour créer des modèles pour les imprimantes 3D FDM, vous devez utiliser une conception assistée par ordinateur (CAO) ou un logiciel d’infographie 3D. Cette technologie présente quelques problèmes avec les pièces creuses, les contre-dépouilles et les surplombs, de sorte que les structures de support telles que les boîtes, les plafonds ou les toiles doivent être conçues et fabriquées pour que les modèles soient imprimés. Heureusement, le logiciel analyse les modèles et, en fonction de leur géométrie, conçoit des structures de support appropriées pour nous. Les imprimantes 3D FDM avec une seule extrudeuse créent des supports à partir du même matériau que l’ensemble du modèle. Dans ce cas, ils doivent être détachés mécaniquement. Les appareils avec extrudeuses doubles ou même plus sont de plus en plus populaires de nos jours. Il permet d’utiliser un matériau de support qui se dissout dans l’eau, mais le processus est assez long, parfois c’est plus que de l’eau que vous devez utiliser, comme un acide citrique. Enfin, tous les matériaux d’impression n’adhèrent pas au matériau de support de dissolution. L’autre facteur important est l’orientation du modèle sur la plateforme du bâtiment. Il doit être organisé de manière à ne pas nécessiter une grande quantité de supports.
Avantages de FDM
• Non toxique, mais certains filaments comme l’ABS produisent des fumées toxiques. Il s’agit généralement d’un processus respectueux de l’environnement.
• Large gamme de matériaux d’impression colorés, pas si chers et avec une utilisation élevée.
• Coûts d’équipement faibles ou modérés.
• Coûts de post-traitement faibles ou modérés (retrait du support et finition de surface).
• Idéal pour les éléments de taille moyenne.
• La porosité des composants est pratiquement nulle.
• Haute stabilité structurelle, propriétés de résistance aux produits chimiques, à l’eau et à la température des matériaux.
• Volume de construction assez important par rapport aux autres technologies de bureau : 600 x 600 x 500 mm.
Inconvénients de FDM
• Options de conception limitées. Impossible de produire des parois minces, des angles aigus, des arêtes vives dans le plan vertical.
• Les modèles imprimés sont les plus faibles dans la direction de construction verticale en raison de l’anisotropie des propriétés du matériau due à la méthode de couche additive.
• Des supports sont nécessaires.
• Pas très précis, avec une tolérance comprise entre 0,10 et 0,25 mm.
• La résistance à la traction est d’environ les deux tiers du même matériau qui a été moulé par injection.
• Difficile de contrôler la température de la chambre de fabrication, ce qui est crucial pour de meilleurs résultats.
• Problème de « marche d’escalier » dans le plan de construction vertical.
SLA – Stéréolithographie
Le deuxième processus le plus populaire appelé SLA (stéréolithographie) fait partie de la photopolymérisation en cuve. Il s’agit de la première technologie AM brevetée. Dans ce processus, une cuve de résine photopolymère est exposée à un faisceau laser ou à un projecteur de lumière numérique. La source d’énergie durcit le matériau couche par couche sur la plateforme. Lorsque cela est fait, la plateforme remonte et une couche de résine inonde la surface. Il est important que la cuve soit fermée pour éviter que les vapeurs de résine ne s’échappent. La chambre elle-même doit être opaque ou teintée pour empêcher la lumière ambiante de durcir prématurément le processus.
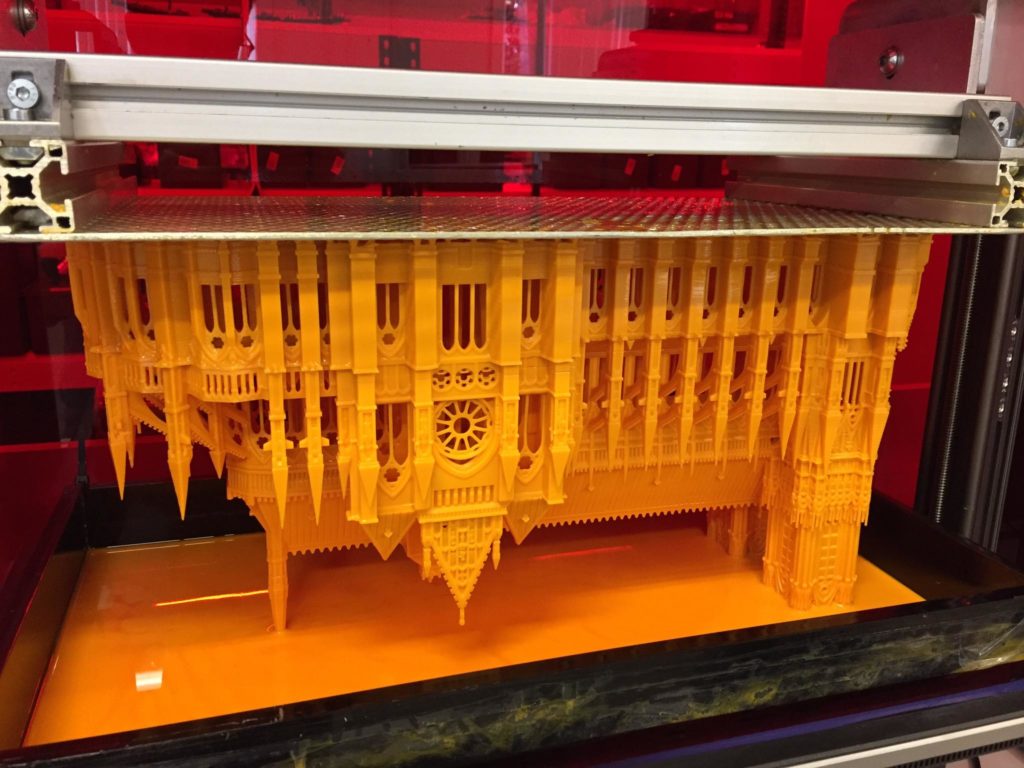
Dans SLA, comme dans FDM, des structures de support sont nécessaires. Mais dans ce cas, ils sont toujours fabriqués à partir du même matériau. Lorsque l’impression est terminée, la pièce terminée est égouttée, lavée dans un solvant qui élimine l’excès de résine et ensuite soumise à la lumière UV pour durcir complètement le composant. Ce n’est qu’alors que les structures de support peuvent être enlevées par découpe.
Avec SLA, vous pouvez imprimer à partir d’une gamme de photopolymères comme l’époxy, l’uréthane, l’acrylate, l’élastomère et le vinyle. Vous pouvez utiliser ces matériaux pour produire des prototypes non fonctionnels, des ajustements et des charnières, des modèles médicaux, en particulier pour les usages dentaires, ainsi que des modèles de moulage.
Conception pour SLA
Lors de la conception de modèles pour SLA, vous devez respecter presque les mêmes règles que la conception pour FDM. En raison des structures nécessaires, la pièce doit être disposée de manière à éliminer les supports redondants, qui dans le SLA peuvent prendre la forme d’âmes, de points, de plafonds ou de goussets. Les pièces finies sont translucides et l’épaisseur de la couche peut être aussi basse que 0,05 – 0,15 mm.
Avantages du SLA
• Excellente finition de surface avec une épaisseur de couche comprise entre 0,05 et 0,15 mm.
• Les pièces finies peuvent être peintes.
• Modérément rapide.
• Économique pour les pièces à faible production (1-20).
• Matériaux pas coûteux
Inconvénients du SLA
• Le post-traitement est un processus nécessaire.
• La résine seule est toxique, mais mélangée à de l’IPA est encore plus dangereuse. Le liquide doit être sécurisé et envoyé pour élimination à une entreprise spécialisée.
• Les déchets ne sont pas recyclables et sont difficiles à gérer
• Les supports sont nécessaires
• Le laser doit être étalonné périodiquement
• L’épaisseur de la couche peut varier dans différentes résines
SLS – Frittage sélectif au laser
SLS représente les processus de fabrication additive sur lit de poudre.
SLS a l’une des plus longues histoires de l’industrie de l’impression 3D, est la plus connue et, aujourd’hui, la technologie de fabrication additive la plus prévisible. La façon dont cela fonctionne est très simple. Un faisceau laser fritte le matériau en poudre dans une chambre scellée, parfois avec une atmosphère de gaz inerte pour empêcher l’oxydation. Lorsque la chambre est préchauffée, juste en dessous de la température de fusion de la poudre, le laser n’est utilisé que pour ajouter un peu d’énergie pour faire fondre la poudre.
Lorsque le frittage de la couche est terminé, les plateformes se repositionnent et un mécanisme dédié reconstitue la couche de poudre d’une chambre d’alimentation dans celle d’impression et le processus est répété. Dans la technologie SLS, aucun support n’est nécessaire car la poudre non frittée, entourant les impressions dans la chambre d’impression, devient elle-même un support.
La précision de la technologie SLS dépend du faisceau laser, de son diamètre et de son acheminement : perpendiculaire à la couche (H-BOT) ou à un angle par rapport à la couche (Galvo). La précision dépend également de la hauteur de la couche. Toute structure solide complexe et compliquée peut être réalisée, même avec des pièces internes mobiles, si seul l’objet conçu permet de se débarrasser de la poudre non frittée à l’intérieur du modèle.
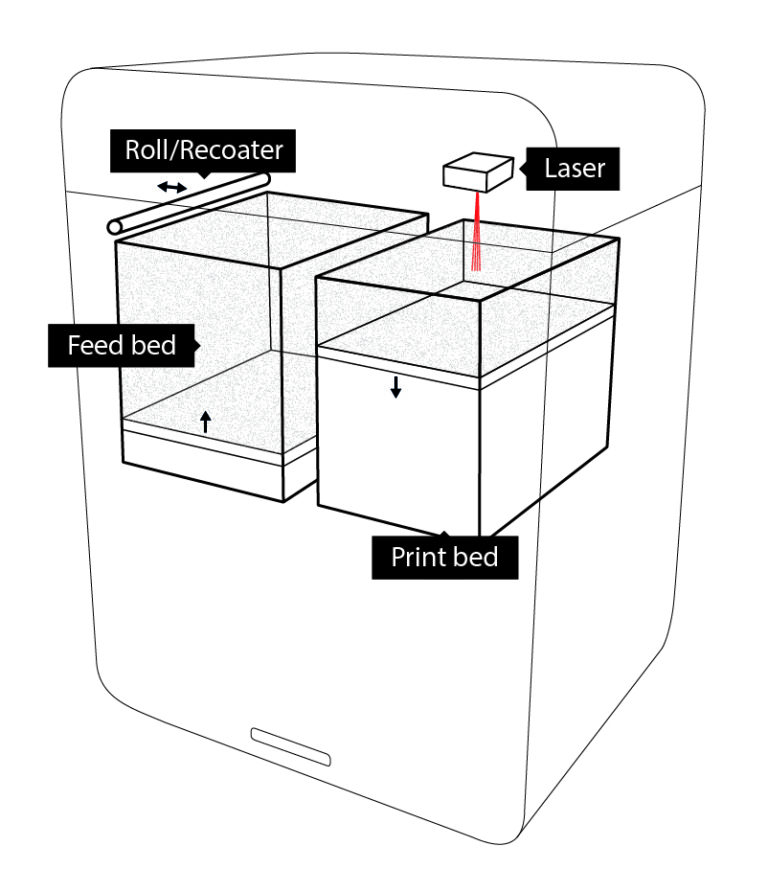
Après l’impression, l’excès de poudre peut être éliminé simplement par aspiration ou brossage. Pour obtenir les meilleurs résultats, l’impression peut également être sablée. Le frittage sélectif au laser utilise une large gamme de matériaux tels que les thermoplastiques, les élastomères et la cire. Certaines machines industrielles fonctionnent sur des métaux en poudre (SLM, DMLS, LPBF) ou des céramiques.
Lorsque nous comparons le nombre d’applications à travers SLS, SLA et FDM, le frittage laser sélectif ouvre certes la liste avec le plus grand nombre d’applications potentielles. Des prototypes fonctionnels et mobiles qui peuvent être testés en soufflerie ou passer d’autres tests expérimentaux, aux composants finaux imprimés en volumes faibles ou modérés. Monter les pièces dans les assemblages, les ajustements par encliquetage et les charnières, l’outillage rapide, les modèles, les noyaux et les moules pour le moulage et le moulage, les modèles de concept de produit, les implants médicaux et dentaires constituent une liste d’utilisations. Il est également utilisé pour les besoins éducatifs, à la fois par les chercheurs et les universitaires pour enseigner aux étudiants.
Conception pour SLS
Les designers choisissent SLS car il leur donne la liberté de forme. La création de pièces mobiles avec une géométrie compliquée est possible. Comme les structures de support ne sont pas nécessaires, il est également plus facile de préparer des projets plus détaillés, avec des arêtes vives et des parois minces. L’épaisseur de couche entre 0,06 et 0,15 mm le rend très précis. De même que dans le cas du FDM et du SLA, l’anisotropie des propriétés du matériau affaiblit la pièce dans la direction verticale de fabrication.
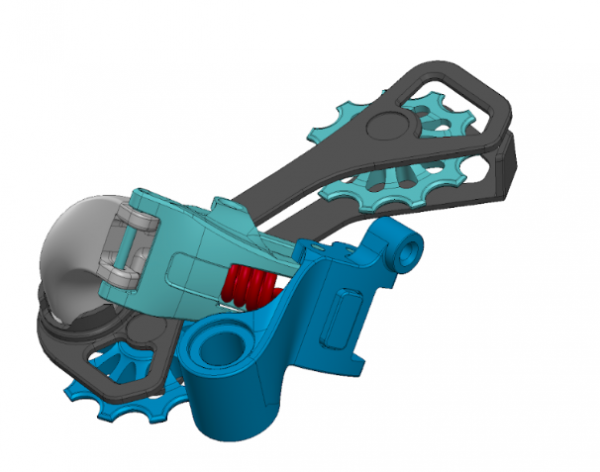
Avantages de SLS
• Aucune structure de support nécessaire.
• Pièces mobiles à géométrie intérieure compliquée.
• Surfaces lisses – il est difficile de remarquer la couche.
• Impressions durables.
• La poudre est réutilisable après impression.
• Coûts de matériaux faibles à modérés, tout en utilisant toute la zone de travail.
• Les imprimantes 3D SLS de bureau sont peu coûteuses par rapport aux machines industrielles.
• Une main-d’œuvre qualifiée n’est pas requise (uniquement les imprimantes 3D SLS de bureau).
Inconvénients de SLS
• Les machines industrielles sont chères.
• Long délai de livraison.
• Le nettoyage de la machine doit être effectué avec précision lors du changement de matériau pour éviter toute contamination.
• Temps d’impression long (pour les objets plus grands).
• Pour une gestion de la poudre pendant le post-traitement, un aspirateur et de l’air comprimé sont recommandés car ils peuvent devenir poussiéreux.